One of the primary advantages of medical plastic injection molding is that it allows for the production of complex geometries and intricate designs with tight tolerances. This is particularly important in the medical industry, where parts and devices must often fit together precisely to function correctly. Injection molding also enables the production of parts with consistent quality and reliability, as each part is produced using the same mold and process.
Another advantage of medical plastic injection molding is that it allows for the use of a wide range of materials, including both thermoplastics and thermosets. This versatility means that medical device manufacturers can select material for the specific application, taking into account factors such as biocompatibility, strength, and durability.
In addition, Medical Plastic Injection Mold Company is a highly efficient manufacturing process, with a relatively low cost per part. This makes it an ideal option for high-volume production runs, such as those required for medical devices that are in high demand.
While medical plastic injection molding offers many advantages, it is not without its challenges. One of the primary challenges is the need to meet strict regulatory requirements, including those set forth by the US Food and Drug Administration (FDA). Medical device manufacturers must demonstrate that their products are safe, effective, and meet all applicable regulations and standards.
Another challenge is the need for specialized equipment and expertise. Medical plastic injection molding requires precise control of temperature, pressure, and other variables to ensure that each part is produced to the desired specifications. It also requires specialized tooling, including molds and dies, that are designed to meet the unique requirements of medical device production.
Finally, medical plastic injection molding can be a complex and time-consuming process, particularly when producing high-precision parts with complex geometries. This can lead to longer lead times and higher production costs, which must be carefully managed to ensure that medical device manufacturers can meet their production targets while maintaining profitability.
Medical plastic injection molding is a critical manufacturing process for the production of high-quality medical devices. While it offers many advantages, including the ability to produce complex geometries and a wide range of materials, it also presents several challenges, including strict regulatory requirements, the need for specialized equipment and expertise, and the potential for longer lead times and higher production costs. As such, medical device manufacturers must carefully weigh the advantages and challenges of medical plastic injection molding when selecting a manufacturing process for their products.
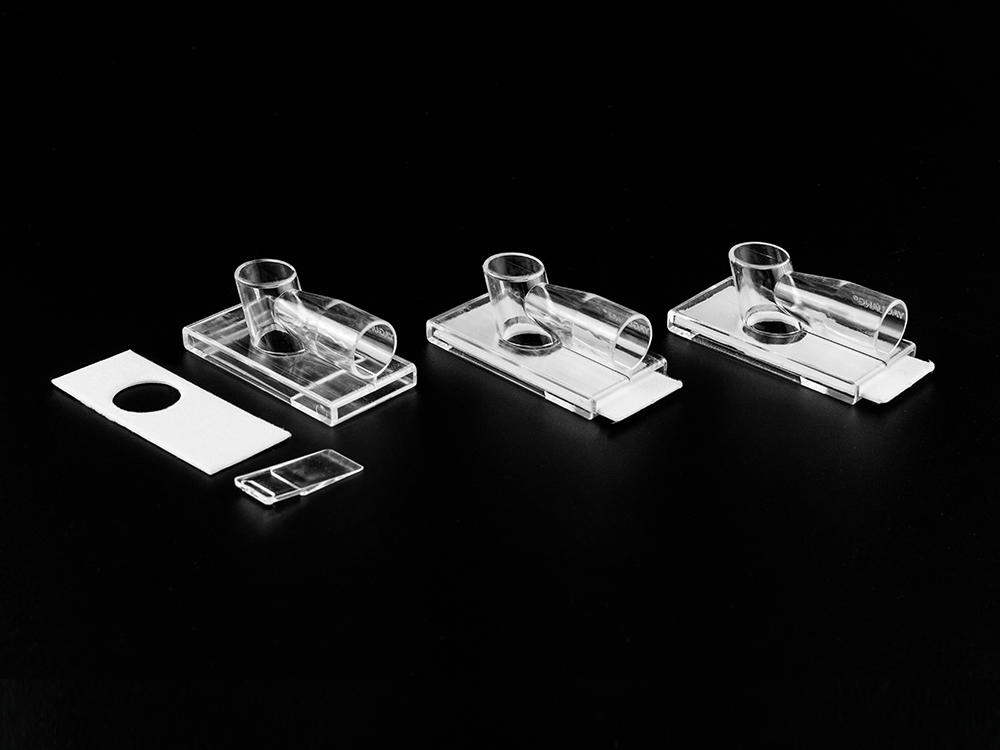
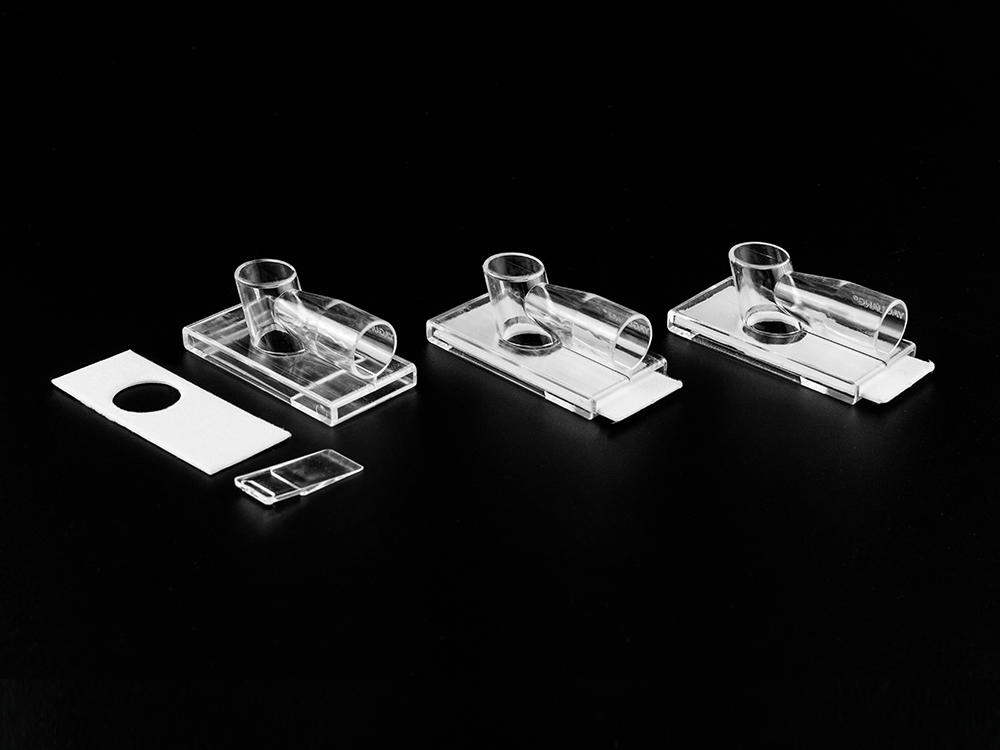
1. L-06 Centrifuge smear slips;
2. The items are transparent;
3. The height is short;
4. The item needs absorbent paper and plastic spacer to match;
5. Can do logo or printing.